Effective inventory management is crucial for businesses in Nigeria looking to improve their order fulfillment processes. By optimizing inventory management, companies can ensure timely deliveries, reduce costs, and improve customer satisfaction.
This step-by-step guide will show you how to use inventory management to improve order fulfillment comprehensively.
- Assess Current Inventory Management Practices
- Implement an Inventory Management System (IMS)
- Set Up Accurate Inventory Tracking
- Establish Inventory Control Policies
- Optimize Warehouse Management
- Forecast Demand Accurately
- Improve Supplier Relationships
- . Leverage Technology
- Train Staff Effectively
- Monitor and analyze performance
- Enhance Customer Communication
- Adopt sustainable practices
- Regulatory Compliance
- Scalability
1. Assess Current Inventory Management Practices
Evaluate Current Systems
Start by reviewing your existing inventory management systems. Identify their strengths and weaknesses to understand what needs improvement. Look at aspects such as the accuracy of your stock levels, the speed of your order processing, and the efficiency of your warehouse operations. Understanding these factors will help you pinpoint areas where enhancements are needed.
For example, this can help you discover where your sales process lags, like late deliveries.
Conduct an Inventory Audit
Perform a thorough inventory audit to accurately understand your current stock levels. This involves counting all inventory items and comparing the physical counts to your recorded inventory data. Identify discrepancies and investigate their causes. Regular audits help maintain accuracy in your inventory records, which is crucial for effective order fulfillment.
Doing this alone can help reveal fraud cases, which Lumi Business inventory software has proven to help mitigate.
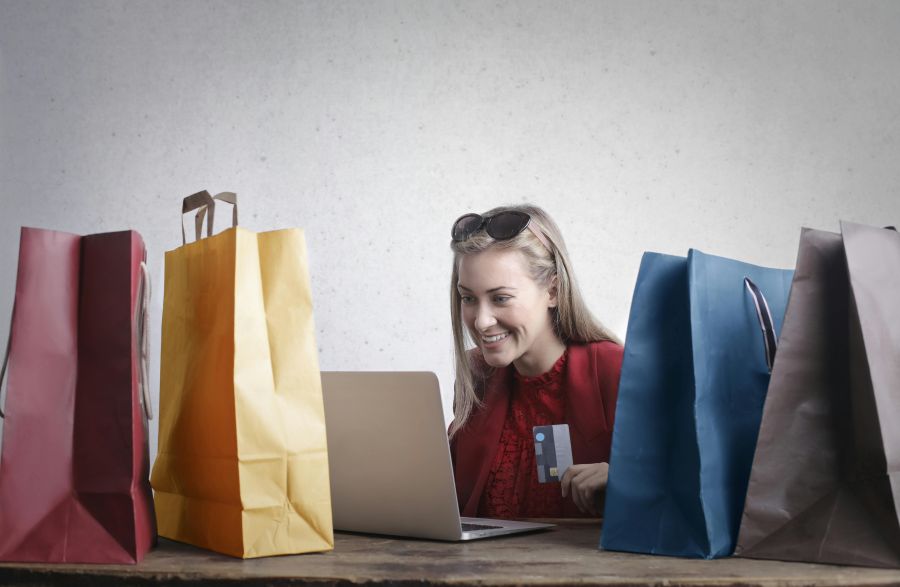
2. Implement an Inventory Management System (IMS)
Select the Right Software
Choose an IMS that fits your business needs. Look for features such as real-time tracking, stock taking, low-stock tracking, and integration capabilities. Real-time tracking helps you maintain up-to-date stock levels, while low-stock tracking ensures that you never run out of high-in-demand products. Integration with other systems like an accounting tool is essential for seamless operations.
Pro Tip: You can consider using Lumi Inventory, a versatile IMS known for its user-friendly interface and robust features. Lumi Inventory offers comprehensive tracking and management capabilities, making it an excellent choice for businesses of all sizes in Nigeria.
3. Set Up Accurate Inventory Tracking
Use Barcodes/RFID
Implement barcode or RFID systems to improve inventory tracking accuracy and efficiency. Barcodes and RFID tags can be scanned quickly, reducing the chances of human error and speeding up the inventory process. These technologies help in maintaining accurate records and tracking items throughout the supply chain.
Regular Stock Counts
Schedule regular cycle counts and annual physical inventory counts. Cycle counts involve counting a portion of your inventory on a rotating basis, which helps in identifying and correcting discrepancies promptly. Annual physical counts provide a comprehensive check of your entire inventory, ensuring long-term accuracy.
4. Establish Inventory Control Policies
Define Stock Levels
Set minimum and maximum stock levels for each product. Minimum stock levels help prevent stockouts, ensuring you always have enough products to meet demand. Maximum stock levels prevent overstocking, which can tie up capital and increase storage costs. Maintaining optimal stock levels helps in balancing supply and demand efficiently.
Reorder Points
Determine reorder points based on lead times and sales velocity. A reorder point is the inventory level at which you need to place a new order to replenish stock before it runs out. Calculating reorder points accurately ensures timely replenishment and prevents stockouts, maintaining a smooth order fulfillment process.
5. Optimize Warehouse Management
Organize Storage
Arrange your warehouse layout logically to enhance storage and retrieval efficiency. Group similar items together, label shelves clearly and ensure high-demand items are easily accessible. An organized warehouse reduces picking times and increases productivity, helping fulfill orders faster.
Implement Picking Strategies
Adopt picking strategies like batch picking, zone picking, or wave picking to streamline the order fulfillment process. Batch picking involves picking multiple orders at once, reducing travel time. Zone picking assigns specific areas to pickers, while wave picking schedules picking tasks to optimize efficiency. These strategies help in improving picking accuracy and speed.
6. Forecast Demand Accurately
Analyze Sales Data
Use historical sales data to predict future demand. Analyzing past sales trends helps identify patterns and forecast future sales more accurately. This information is crucial for maintaining optimal inventory levels and reducing the risk of stockouts or overstocking.
Monitor Market Trends
Stay informed about market trends and seasonal fluctuations. Understanding market dynamics helps you anticipate changes in demand and adjust your inventory levels accordingly. For instance, increasing inventory before a seasonal spike in demand ensures you can meet customer needs without delays.
7. Improve Supplier Relationships
Collaborate with Suppliers
Work closely with your suppliers to ensure timely deliveries and negotiate better terms. Regular communication with suppliers helps in building strong relationships and addressing any issues promptly. Reliable suppliers are essential for maintaining consistent inventory levels and meeting order fulfillment targets.
Vendor Managed Inventory (VMI)
Consider VMI arrangements where suppliers manage your inventory levels. In VMI, suppliers are responsible for maintaining your stock levels based on agreed-upon parameters. This arrangement reduces your burden and ensures a more efficient supply chain, as suppliers are often better positioned to manage inventory replenishment.
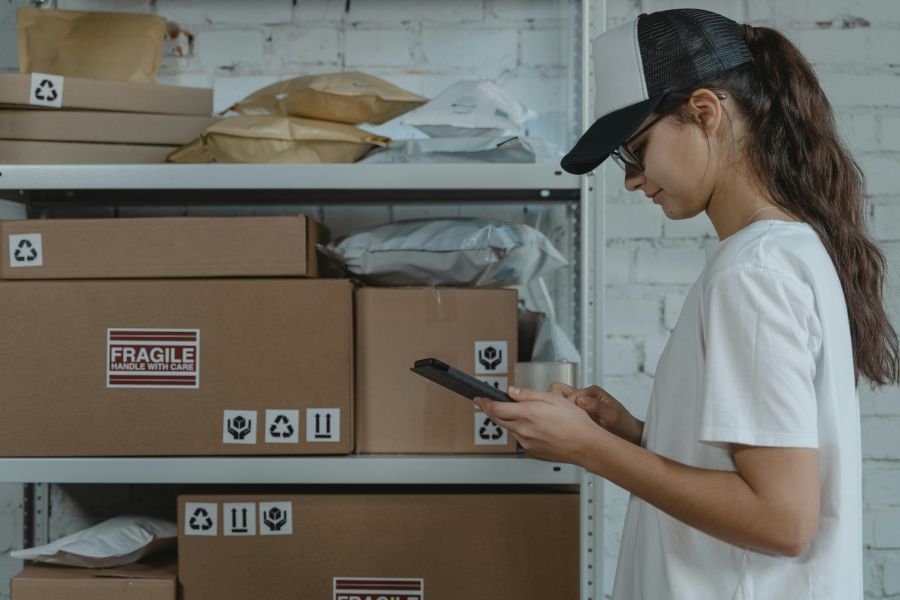
8. Leverage Technology
Use Mobile Solutions
Implement mobile devices for inventory management tasks. Mobile solutions increase efficiency and accuracy in inventory tracking, allowing staff to update inventory data on the go. This real-time data capture helps in maintaining accurate records and speeds up the inventory process.
Cloud-Based Solutions
Utilize cloud-based IMS for real-time access to inventory data from any location. Cloud solutions offer flexibility and enhance data security, as data is stored offsite and can be accessed from anywhere with an internet connection. This is particularly beneficial for businesses with multiple locations or remote teams.
9. Implement Just-In-Time (JIT) Inventory
Minimize Stock Levels
Adopt JIT principles to reduce holding costs and minimize excess inventory. JIT inventory management involves maintaining only as much inventory as needed for immediate production or sales, reducing storage costs, and minimizing waste. This approach requires precise demand forecasting and reliable suppliers.
Coordinate with Suppliers
Ensure that your suppliers can deliver goods quickly and reliably. Effective supplier coordination is essential for JIT inventory management, as any delays can lead to stockouts and disrupt your operations. Establish clear communication channels and contingency plans with your suppliers to mitigate risks.
10. Train Staff Effectively
Ongoing Training
Provide continuous training for staff on inventory management best practices and system usage. Regular training ensures that employees stay updated with the latest procedures and technologies, improving their efficiency and accuracy in managing inventory.
Cross-Training
Train employees to perform multiple roles within the inventory management process. Cross-training increases flexibility and ensures smooth operations during staff shortages or peak periods. Employees with a broad skill set can step in to handle various tasks, maintaining workflow continuity.
11. Monitor and Analyze Performance
KPIs
Track key performance indicators (KPIs) such as inventory turnover, order accuracy, and fulfillment times. KPIs provide measurable data on the effectiveness of your inventory management strategies. Regularly reviewing these metrics helps in identifying areas for improvement and making informed decisions.
Continuous Improvement
Regularly review performance data to identify areas for improvement. Implement necessary changes to enhance your inventory management processes continually. This approach ensures that your strategies evolve with changing business needs and market conditions.
12. Enhance Customer Communication
Order Tracking
Provide customers with real-time order tracking information. Transparency in order tracking improves customer satisfaction, as customers can see the status of their orders and anticipate delivery times. This reduces customer inquiries and enhances their overall experience.
Feedback Loop
Implement a system for collecting and acting on customer feedback. Customer feedback provides valuable insights into the order fulfillment process and highlights areas that need improvement. Addressing customer concerns promptly helps in building trust and loyalty.
13. Adopt Sustainable Practices
Reduce Waste
Implement strategies to minimize waste, such as reducing excess inventory and optimizing packaging. Sustainable practices not only help the environment but also reduce costs associated with storage and disposal of excess stock.
Eco-Friendly Options
Consider eco-friendly packaging and supply chain practices. Using recyclable materials and reducing packaging waste can improve your brand’s reputation and attract environmentally conscious customers.
14. Regulatory Compliance
Stay Informed
Keep up-to-date with local regulations in the state you operate in within Nigeria to ensure your inventory practices comply with the laws. Regulatory compliance helps avoid legal issues and fines and ensures smooth operations. Regularly review and update your practices to align with any changes in regulations.
15. Scalability
Plan for Growth
Ensure your inventory management system can scale with your business as it grows. Scalability is crucial for maintaining efficiency during expansion. Choose systems and processes that can handle increased volume and complexity without compromising performance.
Flexible Systems
Choose systems and processes that can adapt to changes in demand and business size. Flexibility helps in managing growth effectively, allowing your business to respond quickly to market changes and customer needs.
Using inventory management to improve order fulfillment of your business in Nigeria is a multifaceted approach that requires careful planning and execution. This not only boosts efficiency and reduces costs but also improves customer satisfaction and drives business growth.
Ready to improve your order fulfillment, get started with the Lumi Business Inventory management system which powers other retail businesses in Nigeria, just like yours.